Best Parts Inventory Management Software for Your Storeroom Business
Easily track your stock levels with the best parts management inventory software. Read here all about the systems and implementation!
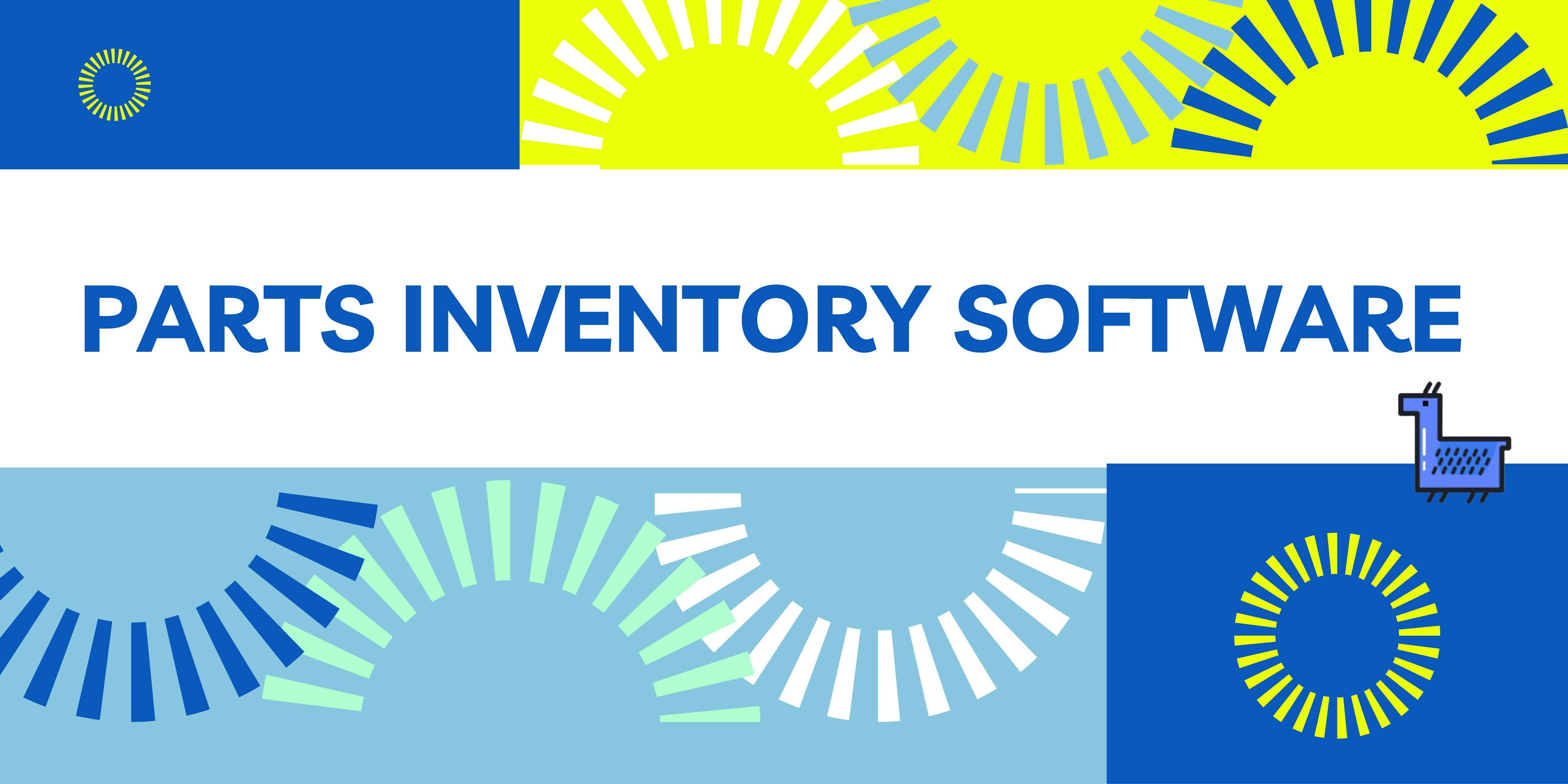
An efficient parts inventory management software is essential if your businesses operates on components, such as a storeroom. It ensures the purchase orders are available when you need them, reduces costs and streamlines operations.
In this article you will find out what is a parts inventory system, how does a CMMS work, and how to implement the software. Also, you will see how to choose the best supplier according to your business needs.
What is a Parts Inventory Management Software?
Companies use parts inventory tools to manage their stock of spare parts and components. It helps keep track of inventory levels, monitor the movement of parts in and out of the warehouse or storage facility. All of that allows businesses to make informed decisions about when to place new orders.
An inventory control system ensures that the right parts are on hand when they are needed. It reduces the risk of stockouts or overstocks and helps streamline the overall operations of the business, without sacrificing quality of inventory items.
Spare parts management inventory can increase productivity, decrease downtime, reduce spending on parts, and boost production. All while having a cloud based, user friendly interface for quick maintenance operations.

Features of a Parts Inventory Software
- Item Identification: This involves assigning a unique identifier to all items of work orders in the inventory system. It includes a part number, a barcode, or an RFID tag. This allows for accurate tracking of parts usage and inventory quantities.
- Inventory Tracking: With this feature, you can track the movement of parts in and out of the stock locations. You can easily record when replacement parts are received, where they are stored, and when they are issued for use.
- Stock Levels: An effective spare parts inventory solution includes tools to monitor work orders in real-time. This helps ensure that the business has the right quantity of parts on hand to prevent overstock and other inventory issues.
- Reordering: When supplies levels fall below a certain point, the system should automatically generate reordering alerts. This way, you can order parts when running low, to replenish the inventory in a timely manner and save time.
- Reporting: An inventory system for spare parts should also provide reporting functionality. So, businesses can analyze the stock levels, parts usage, and ordering trends. This data can help businesses make informed decisions about their inventory management strategies.
- Integration: The inventory management software must integrate with other systems, such as accounting or production tools. It is important because it provides inventory accuracy by streamlining operations and reducing the risk of errors.
All these features are found in our spare parts suppliers, such as UpKeep and Oracle. Continue reading to see what other maintenance solutions they provide and what is the cost of a subscription.
Top 3 Spare Parts Inventory Vendors
Most inventory management vendors also offer asset management tools, making them cost effective for your storeroom business.

Parts Management with UpKeep
Upkeep is a computerized maintenance management system (CMMS) that includes a parts inventory management module. It is designed to track and manage purchase inventory costs, optimize maintenance processes, and improve equipment reliability.
Features:
- Automated reorder points,
- Inventory level monitoring for multiple locations,
- Management of work orders,
- Reporting capabilities of costs and inventory receipts.
Plans and Pricing per user - UpKeep Maintenance
- Starter - $45/ mo
- Professional - $75/ mo
- Business Plus - custom pricing

Oracle Inventory Management
Oracle is a cloud based inventory management module that provides a comprehensive solution for managing stock levels. It helps businesses reduce costs, approve any purchase order, and improve efficiency.
Features:
- Real-time visibility into inventory costs,
- Automatically updated reordering,
- Maintenance departments,
- Integrations with third party software suppliers
Plans and Pricing per user
As Oracle is a vendor in many industries, including hospitality, its plans and pricing differ according to your business needs. To get a quota, you have to contact the representatives yourself.

SAP - Supplier Management
SAP is a leading software vendor that provides a range of enterprise solutions, including inventory management software. It integrates with its ERP (enterprise resource planning) software to generate a suite of management tools, and with other providers.
Features:
- Supply chain management tools,
- Assets management and tracking,
- Increasing visibility through their business technology platform
- Ease of use, flexibility, and customization features.
Plans and Pricing
The cloud based software offers plans for businesses of all sizes and types, including a maintenance storeroom. To get a quota, you have to contact the SAP representatives through live chat, phone, or email.

Benefits of Using an Inventory Management Solution
An efficient parts inventory tool helps ensure that the business has the necessary parts available when needed. This way, it is reducing the risk of delays in production or service delivery.
By having a clear understanding of the parts inventory, businesses can avoid overstocking or understocking. They will not get unnecessary expenses, and will be able to approve needed purchase orders, reducing costs.
A well-designed parts inventory software can streamline business operations. It does it by providing accurate and timely information on stock levels, parts usage, and ordering needs. Saving time, improving efficiency, and reducing the risk of errors at the same time.
Customer support is a very important characteristic of any maintenance storeroom. A spare parts inventory manager ensures that businesses have the necessary parts to fulfill orders or repair products quickly and efficiently so they don't lose money or clients.
With accurate and up-to-date information on stock and parts usage, businesses can make informed decisions about when to order new parts and the minimum quantity to order so they don't encounter issues.
Other benefits of using a high rated parts inventory software are:
- Real-time inventory updates
- Set minimum stock quantities
- Organize and use inventory
- Record vendor information in one place
- Forecast the parts you'll need for future work
- Stay ahead on preventive maintenance
- View, sort, and explore all your parts data
- Inventory tracking and reporting

Challenges and Pitfalls of a Parts Inventory Software
Although the benefits heavily outweigh the challenges, there are some disadvantages to using a spare parts management system.
Data accuracy
One of the key challenges in implementing a parts inventory software is ensuring the accuracy of the data entered into the system. If the inventory data is not entered correctly or updated regularly, it can lead to inaccurate inventory levels.
To avoid this, businesses need to establish data entry protocols and implement regular audits to ensure data accuracy.
Integration and cost
Integrating the parts inventory software with systems such as ERP, purchasing, and accounting can be a complex and time-consuming process. Organizations need to ensure that the software is compatible with their existing systems and that data can be shared seamlessly between them.
Implementing a spare parts manager can be expensive, especially for small businesses. To avoid extra costs, carefully evaluate implementation and maintaining expenses, and determine if it is worth it on the long run.
Staff training
Employees who will be using the parts management system need to be trained on how to use it effectively. This training can be time-consuming and expensive, and if not done properly, can result in inefficiencies and human error.
Many inventory control tools offer online trainings done by technicians, or guide posts for you to manage the onboarding period and money spent.
System downtime
Any downtime in the parts inventory software can result in delays in maintenance operations. It can be costly for the business, so you need to ensure that the software is reliable and has minimal downtime.
Think about implementing a regular maintenance team to perform backups, and use redundancy and failover systems.

Best Practices in Implementing an Inventory Control Software
Implementing an inventory control software can provide numerous benefits to businesses, such as reducing costs, improving efficiency, and increasing accuracy. To ensure a successful implementation and usage of the software, here are some best practices your parts managers should follow:
Evaluate your business needs and the solutions available
Before implementing an inventory software, conduct a thorough needs assessment to determine the specific requirements of your business. Identify your goals, current inventory management processes, and any pain points that need to be addressed.
Then, evaluate different software options when choosing a spare parts management solution. Make sure you consider factors such as cost, ease of use, scalability, and mobile device functionality in your decision.
Strategise and train
Develop a data management strategy that outlines how information will be collected, stored, and maintained. Ensure that data is entered accurately and regularly updated to ensure inventory accuracy. Think about creating schedules for your maintenance storeroom, so you can track performance.
Ensure that employees who will be using the inventory control software are properly trained on how to use the system effectively. This includes training on work orders entry, reporting, and analysis.
Implement, Monitor, and Improve
Implement proper controls, such as security measures, access controls, and backup procedures to protect inventory and ensure system uptime.
Identify trends, make informed decisions, and optimize inventory management processes through monitoring stock.
Continuously review and improve inventory management processes based on data analysis and feedback from employees to ensure maximum efficiency and accuracy.